COMPARISON BETWEEN ALLOYS
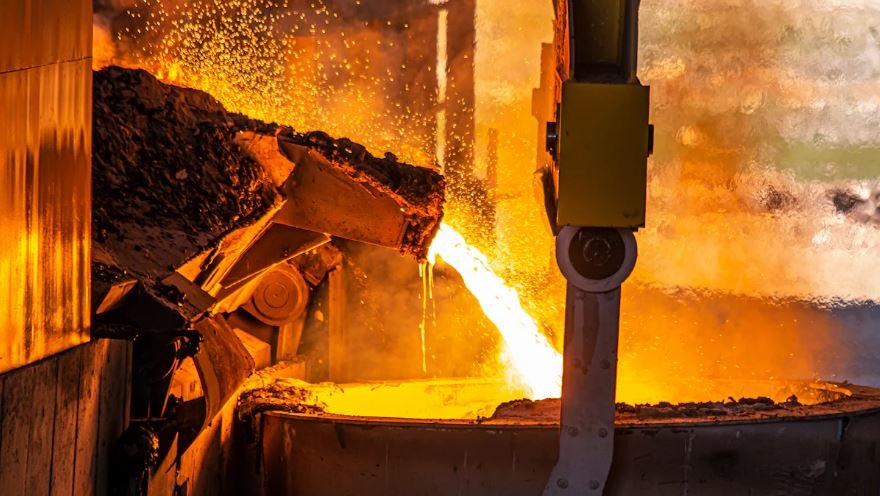
Aluminium Alloys 6061 vs 6082
Aluminium alloys 6061 and 6082 are both popular choices for structural applications due to their excellent mechanical properties, weldability, and corrosion resistance. While they share many similarities, there are also some differences that may influence the choice between them for specific applications. Here’s a detailed comparison between aluminium alloys 6061 and 6082:
- Chemical Composition:
- 6061: Aluminium alloy 6061 is a heat-treatable alloy with the following typical composition:
- Aluminium (Al): Balance
- Magnesium (Mg): 0.8% – 1.2%
- Silicon (Si): 0.4% – 0.8%
- Iron (Fe): 0.7% max
- Copper (Cu): 0.15% – 0.4%
- Zinc (Zn): 0.25% max
- Titanium (Ti): 0.15% max
- Chromium (Cr): 0.04% – 0.35%
- Other elements: 0.05% max (each), 0.15% max (total)
- 6082: Aluminium alloy 6082 is also heat-treatable and has a composition similar to 6061, with some differences:
- Aluminium (Al): Balance
- Magnesium (Mg): 0.6% – 1.2%
- Silicon (Si): 0.7% – 1.3%
- Iron (Fe): 0.5% max
- Copper (Cu): 0.1% max
- Manganese (Mn): 0.4% – 1.0%
- Chromium (Cr): 0.25% max
- Other elements: 0.05% max (each), 0.15% max (total)
- 6061: Aluminium alloy 6061 is a heat-treatable alloy with the following typical composition:
- Mechanical Properties:
- Both 6061 and 6082 alloys offer high strength and good machinability after heat treatment.
- The tensile strength and yield strength of 6082 are slightly higher than those of 6061, especially in the T6 temper.
- Weldability:
- Both alloys have good weldability using common welding methods such as TIG (tungsten inert gas) and MIG (metal inert gas) welding.
- However, some users suggest that 6061 may have slightly better weldability due to its lower magnesium content.
- Corrosion Resistance:
- Both alloys offer good corrosion resistance, although they may not be as corrosion-resistant as some other aluminium alloys like 5052 or 5083.
- The addition of magnesium in both alloys enhances their resistance to stress corrosion cracking.
- Applications:
- 6061: This alloy is commonly used in structural applications such as aircraft components, marine fittings, bicycle frames, automotive parts, and structural sections.
- 6082: It is often preferred for applications requiring higher strength and better corrosion resistance, such as architectural structures, marine components, and transportation equipment.
- Availability and Cost:
- Both alloys are readily available in various forms such as sheets, plates, bars, and extrusions.
- The cost of both alloys may vary depending on factors such as market demand, production volume, and alloying elements.
In summary, while aluminium alloys 6061 and 6082 share many similarities in terms of composition, mechanical properties, and applications, there are some differences that may influence the choice between them for specific applications. Users should consider factors such as required strength, corrosion resistance, weldability, and cost when selecting the most suitable alloy for their application. Consulting with material suppliers or engineers can provide further guidance based on specific requirements.
Aluminium Alloys 7075 vs 2014
Aluminium alloys 7075 and 2014 are both high-strength aerospace-grade alloys with excellent mechanical properties, but they have some differences in composition, characteristics, and applications. Here’s a detailed comparison between aluminium alloys 7075 and 2014:
- Chemical Composition:
- 7075: Aluminium alloy 7075 is a high-strength alloy primarily composed of aluminium, zinc, copper, and small amounts of other elements:
- Aluminium (Al): Balance
- Zinc (Zn): 5.1% – 6.1%
- Magnesium (Mg): 2.1% – 2.9%
- Copper (Cu): 1.2% – 2.0%
- Chromium (Cr): 0.18% – 0.28%
- Other elements: 0.05% max (each), 0.15% max (total)
- 2014: Aluminium alloy 2014 is also a high-strength alloy with a similar composition to 7075 but with lower zinc content and higher copper content:
- Aluminium (Al): Balance
- Copper (Cu): 3.9% – 5.0%
- Magnesium (Mg): 0.2% – 0.8%
- Silicon (Si): 0.4% – 0.8%
- Iron (Fe): 0.7% max
- Manganese (Mn): 0.4% – 1.2%
- Other elements: 0.05% max (each), 0.15% max (total)
- 7075: Aluminium alloy 7075 is a high-strength alloy primarily composed of aluminium, zinc, copper, and small amounts of other elements:
- Mechanical Properties:
- 7075: Alloy 7075 is known for its exceptional strength-to-weight ratio, making it one of the strongest aluminium alloys available. In the T6 temper, it offers high tensile strength and excellent resistance to fatigue and stress corrosion cracking.
- 2014: While not as strong as 7075, alloy 2014 still offers good strength and excellent machinability. It has slightly lower tensile strength and fatigue resistance compared to 7075 but is easier to machine.
- Machinability:
- 7075: Alloy 7075 has poor machinability in its annealed state but can be machined effectively after heat treatment.
- 2014: Alloy 2014 is known for its excellent machinability, making it a preferred choice for applications requiring intricate machining operations.
- Corrosion Resistance:
- 7075: This alloy has good corrosion resistance, particularly in outdoor and marine environments. However, it may not be as corrosion-resistant as some other aluminium alloys like 6061 or 5052.
- 2014: Alloy 2014 offers moderate corrosion resistance but may require protective coatings or treatments for extended outdoor exposure.
- Applications:
- 7075: Alloy 7075 is commonly used in aerospace applications such as aircraft structures, fuselage frames, wing spars, and missile components. It is also used in high-performance sporting goods and automotive components.
- 2014: Alloy 2014 is often used in applications requiring high strength and good machinability, such as aerospace fittings, hydraulic valve bodies, structural components, and precision parts for the automotive and machinery industries.
- Availability and Cost:
- Both alloys are readily available in various forms such as sheets, plates, bars, and extrusions.
- The cost of 7075 is typically higher than that of 2014 due to its higher strength and demand in aerospace and high-performance applications.
In summary, aluminium alloys 7075 and 2014 are both high-strength alloys with excellent mechanical properties, but they differ in composition, machinability, corrosion resistance, and specific applications. When selecting between them, consider factors such as required strength, machinability, corrosion resistance, and application requirements. Consulting with material suppliers or engineers can provide further guidance based on specific needs.
Stainless Steel Grades 303 vs 304
Stainless steel grades 303 and 304 are both popular choices for various applications, but they differ in terms of composition, properties, and suitability for specific uses. Here’s an overview of the differences between these two grades:
- Chemical Composition:
- SS303: Stainless steel grade 303 contains added sulfur and selenium, which improve machinability but decrease corrosion resistance compared to other stainless steel grades. It typically contains around 17-19% chromium and 8-10% nickel.
- SS304: Stainless steel grade 304 is a more versatile and widely used grade. It contains higher chromium content (around 18-20%) and nickel content (around 8-10%) compared to SS303, which provides superior corrosion resistance and makes it suitable for a broader range of applications.
- Corrosion Resistance:
- SS303: While SS303 offers decent corrosion resistance, it is not as corrosion-resistant as SS304. The addition of sulfur and selenium can lead to reduced resistance to certain corrosive environments, particularly in chloride-rich or acidic conditions.
- SS304: SS304 is highly resistant to corrosion in various environments, including atmospheric conditions, freshwater, mild acids, and alkalis. Its superior corrosion resistance makes it suitable for use in applications where exposure to corrosive elements is a concern, such as marine environments and food processing.
- Machinability:
- SS303: Stainless steel grade 303 is specifically designed for improved machinability, thanks to the addition of sulfur and selenium. It is easier to machine compared to SS304, making it a preferred choice for applications that require extensive machining operations, such as screw machining and CNC machining.
- SS304: While SS304 is not as easily machinable as SS303, it still offers good machinability characteristics, especially when compared to other austenitic stainless steel grades. However, it may require slower machining speeds and more rigid tooling compared to SS303.
- Applications:
- SS303: Stainless steel grade 303 is commonly used in applications where extensive machining is required, such as shafts, nuts, bolts, and fittings. It is also used in applications where moderate corrosion resistance is acceptable, such as in certain automotive components and machining equipment.
- SS304: SS304 finds widespread use across various industries due to its superior corrosion resistance and versatility. It is commonly used in food processing equipment, architectural components, kitchen appliances, chemical processing equipment, and pharmaceutical machinery.
In summary, while both SS303 and SS304 are stainless steel grades with their own unique properties and advantages, SS304 generally offers superior corrosion resistance and broader applicability compared to SS303. SS303 is favored for its improved machinability, particularly in applications requiring extensive machining operations. The choice between these grades depends on the specific requirements of the application, including factors such as corrosion resistance, machinability, and cost considerations.
Stainless Steel Grades 304 vs 304L
Stainless steel grades 304 and 304L are both austenitic stainless steels, but they have subtle differences in their composition and properties. Here’s an overview of the distinctions between these two grades:
- Chemical Composition:
- SS304: Stainless steel grade 304 contains around 18-20% chromium and 8-10.5% nickel, along with small amounts of carbon, manganese, silicon, phosphorus, sulfur, and nitrogen. It is the most widely used stainless steel grade and offers good corrosion resistance, strength, and formability.
- SS304L: Stainless steel grade 304L is a low-carbon variant of SS304, with a maximum carbon content of 0.03%. This lower carbon content minimizes carbide precipitation during welding, which reduces the risk of intergranular corrosion. Otherwise, the composition of SS304L is similar to SS304.
- Carbon Content:
- SS304: SS304 can contain higher levels of carbon compared to SS304L, typically up to 0.08%.
- SS304L: SS304L is specifically designed to have a lower carbon content, typically limited to a maximum of 0.03%. This low carbon content helps prevent sensitization and subsequent intergranular corrosion during welding and other thermal processes.
- Weldability and Corrosion Resistance:
- SS304: While SS304 offers excellent corrosion resistance in most environments, it is susceptible to sensitization—a condition where chromium carbide precipitation occurs at the grain boundaries, leading to intergranular corrosion in certain corrosive environments.
- SS304L: SS304L is more resistant to sensitization and intergranular corrosion due to its lower carbon content. It is preferred for applications involving welding or prolonged exposure to elevated temperatures, where sensitization is a concern.
- Applications:
- SS304: Stainless steel grade 304 is widely used in various industries and applications, including food processing equipment, kitchen appliances, architectural components, chemical processing equipment, and pharmaceutical machinery.
- SS304L: SS304L is particularly suitable for applications where welding is required, such as welded components, tanks, pipes, and pressure vessels. It is also used in environments where sensitization and intergranular corrosion must be minimized, such as in chemical processing and petrochemical industries.
In summary, while SS304 and SS304L are both austenitic stainless steels with similar compositions, the lower carbon content of SS304L provides improved resistance to sensitization and intergranular corrosion. SS304L is preferred for applications involving welding or exposure to elevated temperatures where sensitization may occur. Ultimately, the choice between these grades depends on the specific requirements of the application, including considerations of weldability, corrosion resistance, and mechanical properties.